
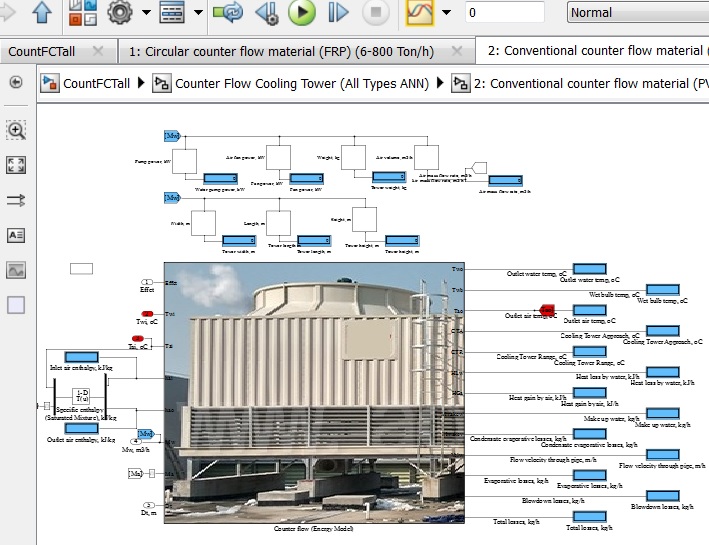
The only difference is the Chilled water pumps section in Chilled water loop tab of the Chilled water loop dialog will now have a new parameter: Loop configuration, which will have two options: Primary-Secondary and Primary only. will be calculated to be zero (leaving the secondary pump with variable flow to be seen as the only active pump and therefore the “primary” pump), this will be represented in exactly as it was in older versions of ApacheHVAC. When loading an older network with a secondary-only variable flow pump configuration that was used to model a variable-flow primary-only configuration wherein both the primary and secondary pumps are technically still present on the loop, but the specific pump power of the primary pump in this configuration is set to zero so that all primary pump power, pump heat gain, pump temperature rise etc. The Explicit heat transfer model can be used only with explicit modeling of the loop water temperatures on the heat recovery source and recipient sides-i.e., with the condenser water loop model as source and hot water loop or heat transfer loop model as the recipient.
#COOLING TOWER DESIGN CALCULATION SOFTWARE UPGRADE#
In the explicit heat transfer model, the water-to-water heat pump (WWHP) used to upgrade the heat recovery is enhanced by the inclusion of a COP that varies according to thermal lift between the heat recovery source loop and recipient loops during the simulation: Linear interpolation is applied to 1/COP to modulate between two heat pump COP values corresponding to two operational data points specified by the user (low thermal lift and high thermal lift). It transfers heat between the source and recipient loops using an explicit water-to-water heat exchanger model with effectiveness that is continuously modulated for off-design temperature differences across the heat exchanger. The Percentage of heat rejection model can be used regardless of whether there is an explicit modeling of the loop water temperatures on the heat recovery source and recipient sides.Įxplicit heat transfer : This more detailed heat recovery model was added in v6.5. Therefore, when serving space-heating loads, such as airside heating coils and baseboard heaters that require higher temperatures than normally available via a heat exchanger on the condenser water loop, this simple WSHP option can be used to account for energy used to upgrade the temperature (e.g., from 90☏ to 140☏). This would be used for adding recovered heat to hot water loops with higher temperatures-i.e., hotter than the condenser loop, in contrast to low-temperature hot-water heating systems for hydronic radiant floors, DHW pre-heat, or similar. The temperature for the recovered heat can be upgraded with an electric water-to-water or water-source heat pump (WSHP). The fixed percentage represents simple heat-exchanger effectiveness. It models the heat recovery as a simple percentage of the source heat rejection, with optional constant-COP water-source heat pump for upgrading the transferred heat. Please have a look at this Bentley Communities wiki mentioned for further information regarding this topic.Percentage of heat rejection : This is essentially the old heat recovery model provided in pre-v6.5 versions. Wind load on plate element Further Reading Demonstration of Wind Load on Cooling Tower in STAAD.Pro **Note: Wind definition is not needed in this case as the wind pressure is manually calculated depending on intensity vs height table along with the consideration of other wind load calculation parameter. In this model, pressure load in added in positive X and Z direction. Finally, we will add pressure loads to the plate element.Next, we will assign supports to the base co-ordinate of the model.A plate thickness of 450mm is added to this model.

Secondly, we will add properties to the model.We can even customize the dimension according to the requirement.
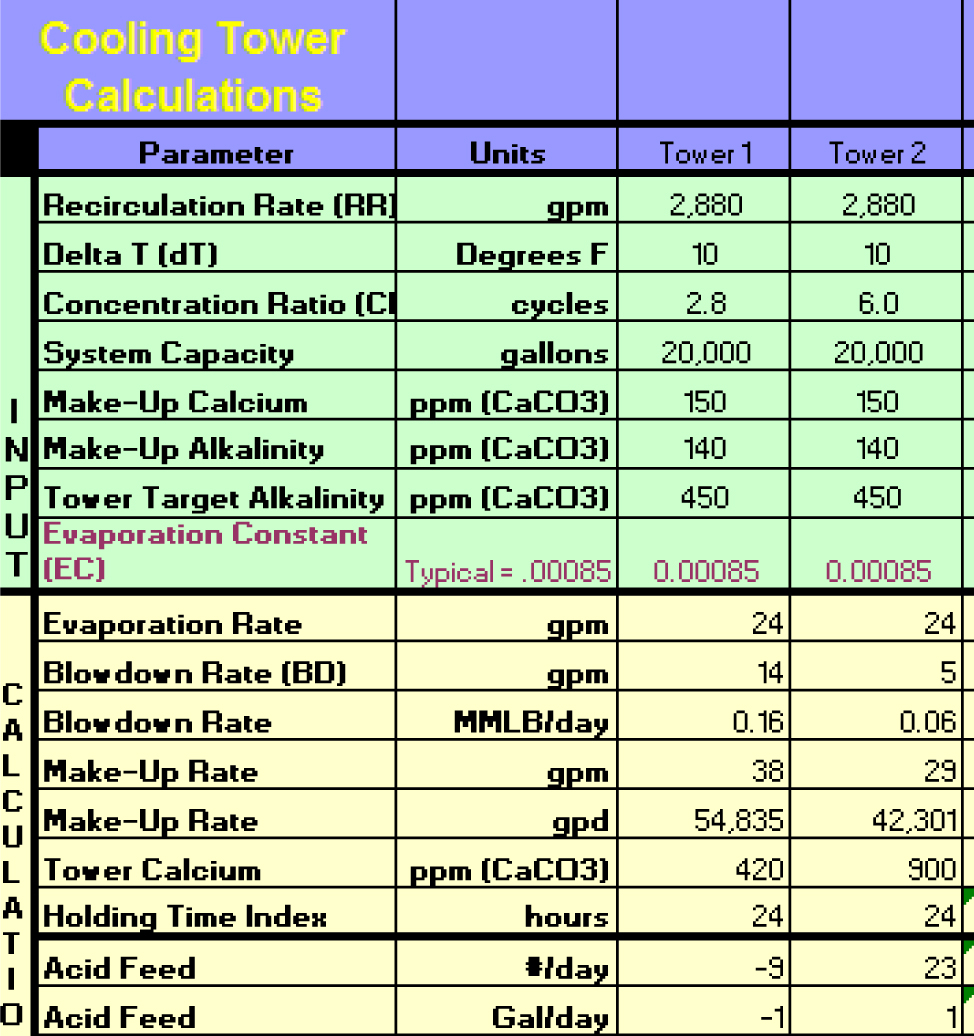

Listed below are the solution to this problem. Wind load on Cooling tower – (Plate element) Solution Hence wind load can not be automatically generated in this case. The cooling tower prototype available within “Structure Wizard” in STAAD.pro consists of plate elements. This is because automatic generation of wind load can only on beam members forming closed panel.
